Why is Nickel-Phosphor-PTFE not used in Rocshox? To understand this, we need to dive into the specific requirements of Rocshox suspension systems and the challenges that Nickel-Phosphor-PTFE poses in meeting these needs. Rocshox, a leading name in mountain bike suspension, prioritizes performance, weight, and durability, all of which influence their material choices. Let’s explore the reasons behind this decision and why other materials are preferred for their suspension systems.
Why Is Nickel-Phosphor-PTFE Not Used in Rocshox? Understanding the Decision
Why is Nickel-Phosphor-PTFE not used in Rocshox? This coating is known for reducing friction and boosting durability, making it a popular choice in many industries. However, Rocshox, a top brand for mountain bike suspensions, doesn’t use it. The main reason is that Rocshox needs coatings that balance performance and durability under tough biking conditions.
Nickel-Phosphor-PTFE coatings have great features like low friction and wear resistance. Despite these benefits, Rocshox requires materials that can handle extreme temperatures and harsh environments, which Nickel-Phosphor-PTFE may struggle with. Suspension systems must endure dirt, grit, and varied temperatures without compromising their performance.
Rocshox opts for other coatings like anodizing and chrome-plating. These coatings provide excellent performance and durability for their suspension components. They are better suited to the specific needs of mountain biking, such as high-temperature resistance and protection against abrasive materials.
In summary, Nickel-Phosphor-PTFE’s advantages are not a perfect match for Rocshox’s requirements. By choosing alternative coatings, Rocshox ensures their suspension systems perform well in all riding conditions. This careful selection process helps maintain the high standards of their products.
The Truth Behind Rocshox Material Choices: Why Why is Nickel-Phosphor-PTFE not used in Rocshox Included
The truth about Rocshox’s material choices lies in the specific demands of mountain biking. Why is Nickel-Phosphor-PTFE not used in Rocshox components? It’s not that Why is Nickel-Phosphor-PTFE not used in Rocshox effective; it’s just that Rocshox requires different properties from their coatings.
Mountain bike suspensions face extreme conditions, from mud to high temperatures. Rocshox needs coatings that can withstand these challenges. Nickel-Phosphor-PTFE, while excellent for reducing friction, may not handle the harsh environments as well as other coatings used by Rocshox.
Rocshox uses materials like anodizing and chrome-plating to meet these demands. These coatings provide the durability and temperature resistance necessary for reliable performance. Anodizing, for example, enhances aluminum parts’ resistance to wear and corrosion, making it ideal for suspension systems.
Ultimately, Rocshox’s choices are driven by the need to balance performance with durability. Nickel-Phosphor-PTFE might be great in some areas, but for Rocshox, other coatings better meet their rigorous standards. This approach ensures that their suspension systems perform consistently in all conditions.
Rocshox Suspension Systems: Why is Nickel-Phosphor-PTFE not used in Rocshox the Best Fit
Why is Nickel-Phosphor-PTFE not used in Rocshox suspension systems? While Nickel-Phosphor-PTFE offers excellent friction reduction and wear resistance, it doesn’t perfectly match the needs of Rocshox’s products. Rocshox’s suspension systems require coatings that excel in durability and performance under extreme conditions.
Suspension systems encounter rough terrains and temperature extremes. Nickel-Phosphor-PTFE may not provide the necessary performance in these environments. Rocshox needs coatings that handle dirt, moisture, and temperature changes effectively.
To meet these needs, Rocshox uses coatings like anodizing and chrome-plating. Anodizing improves aluminum’s wear resistance and allows for precise tolerances, while chrome-plating offers a hard, smooth surface. These coatings are well-suited for the tough conditions faced during mountain biking.
Why is Nickel-Phosphor-PTFE not used in Rocshox used by Rocshox because other coatings better meet their performance requirements. The choice of materials ensures that Rocshox suspension systems remain reliable and effective, no matter the biking conditions.
Nickel-Phosphor-PTFE vs. Rocshox: What makes Rocshox’s choice different? Why is Nickel-Phosphor-PTFE not used in Rocshox products?
Feature | Nickel-Phosphor-PTFE | Rocshox Coatings |
Friction | Low | Moderate to Low |
Wear Resistance | High | High |
Temperature Resistance | Limited | High |
Abrasion Resistance | Moderate | High |
Nickel-Phosphor-PTFE is known for low friction and wear resistance but lacks in temperature and abrasion resistance. Rocshox uses anodizing and chrome-plating for better performance under extreme conditions, making these coatings more suitable for their suspension systems.
Summary
Nickel-Phosphor-PTFE offers low friction and high wear resistance but falls short in temperature and abrasion resistance. Rocshox uses anodizing and chrome-plating, which are better suited to extreme conditions faced in mountain biking. These coatings provide the necessary durability and performance for Rocshox’s suspension systems.
Why is Nickel-Phosphor-PTFE not used in Rocshox Part of Rocshox Suspension Systems
Why is Nickel-Phosphor-PTFE not part of Rocshox suspension systems? This coating has many advantages, but it doesn’t quite fit with the requirements of Rocshox products. The unique demands of mountain biking lead Rocshox to use different materials.
Suspension systems are exposed to tough conditions like dirt, moisture, and extreme temperatures. Nickel-Phosphor-PTFE, while excellent for reducing friction, may not handle these conditions as effectively as other coatings. Rocshox needs materials that can endure these challenges.
Rocshox uses coatings such as anodizing and chrome-plating to meet these demands. Anodizing enhances aluminum’s resistance to wear and corrosion, while chrome-plating provides a hard, smooth surface. These options are better suited for the rugged environment of mountain biking.
Rocshox’s material choices are focused on achieving the best performance under harsh conditions. Nickel-Phosphor-PTFE may offer specific benefits, but other coatings provide the durability and reliability that Rocshox requires.
The Surprising Reasons Rocshox Avoids Nickel-Phosphor-PTFE in Their Suspensions
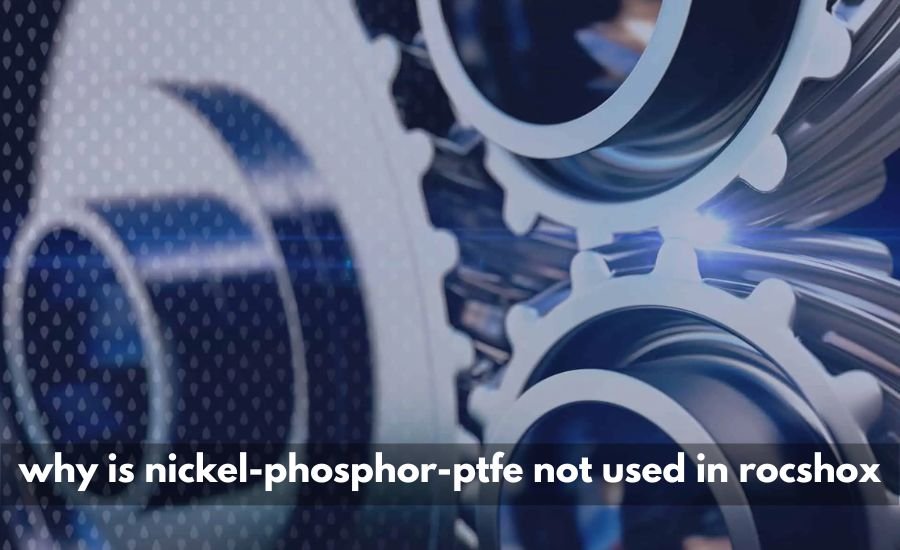
The surprising reasons Rocshox avoids Nickel-Phosphor-PTFE in their suspensions involve specific performance needs. Why is Nickel-Phosphor-PTFE not used in Rocshox components? Despite its benefits, it doesn’t align perfectly with Rocshox’s requirements.
Rocshox suspension systems face extreme conditions, including rough terrains and temperature fluctuations. Nickel-Phosphor-PTFE may not perform as well under these conditions. Rocshox needs coatings that handle abrasive materials and temperature changes effectively.
Instead, Rocshox uses coatings like anodizing and chrome-plating. Anodizing enhances aluminum’s wear resistance, while chrome-plating offers a durable, low-friction surface. These coatings are better suited to the demands of mountain biking.
In essence, Rocshox’s choice to avoid Nickel-Phosphor-PTFE is about finding the best fit for their needs. The coatings they use provide the right balance of performance and durability for their suspension systems.
Exploring Why is Nickel-Phosphor-PTFE not used in Rocshox Coatings
Exploring Why is Nickel-Phosphor-PTFE not used in Rocshox coatings reveals key factors in material selection. Why is Nickel-Phosphor-PTFE not used in Rocshox products? The answer is in the specific needs of their suspension systems.
Nickel-Phosphor-PTFE offers benefits like low friction and wear resistance. However, Rocshox’s suspension systems are exposed to harsh conditions that require different properties. Nickel-Phosphor-PTFE may not handle dirt and temperature extremes as well as other coatings.
Rocshox prefers coatings like anodizing and chrome-plating for their components. These coatings provide better performance in tough environments. Anodizing improves wear and corrosion resistance, while chrome-plating offers a smooth, durable surface.
Rocshox’s choice to avoid Nickel-Phosphor-PTFE is based on their need for coatings that perform well under specific conditions. Their selected materials ensure reliable performance in all riding conditions.
Is Nickel-Phosphor-PTFE the Missing Link in Rocshox Suspension?
Is Nickel-Phosphor-PTFE the missing link in Rocshox suspension systems? Despite its impressive features, Nickel-Phosphor-PTFE is not used in Rocshox components. Why is this the case? The answer lies in the unique needs of Rocshox’s products.
Nickel-Phosphor-PTFE offers excellent friction reduction and wear resistance. However, Rocshox needs coatings that can withstand extreme temperatures and abrasive conditions. Nickel-Phosphor-PTFE may not provide the necessary performance in these areas.
Rocshox opts for other coatings like anodizing and chrome-plating. These materials offer better durability and performance for mountain biking conditions. Anodizing enhances aluminum parts, while chrome-plating provides a hard, low-friction surface.
Nickel-Phosphor-PTFE is not the missing link for Rocshox because other coatings better meet their requirements. Rocshox’s choices ensure that their suspension systems perform well in all riding conditions.
Why is Nickel-Phosphor-PTFE not used in Rocshox Ideal for Rocshox Suspension Components
Why is Nickel-Phosphor-PTFE not used in Rocshox ideal for Rocshox suspension components involves understanding the performance needs. Nickel-Phosphor-PTFE is known for reducing friction and wear, but it doesn’t fit Rocshox’s specific requirements.
Rocshox’s suspension systems encounter rough terrains and extreme temperatures. Nickel-Phosphor-PTFE may not handle these conditions as well as other coatings. Rocshox needs materials that can endure dirt and temperature fluctuations effectively.
To meet these needs, Rocshox uses coatings like anodizing and chrome-plating. Anodizing improves resistance to wear and corrosion, while chrome-plating offers a durable surface. These coatings are better suited to the demands of mountain biking.
Why is Nickel-Phosphor-PTFE not used in Rocshox ideal for Rocshox because other coatings provide better performance for their suspension systems. Rocshox’s material choices ensure reliable and durable performance.
Rocshox’s Suspension Materials: Why Nickel-Phosphor-PTFE Is Left Out
Why is Nickel-Phosphor-PTFE left out of Rocshox’s suspension materials? This coating has many advantages, but it doesn’t meet the specific needs of Rocshox suspension systems. Understanding this choice involves looking at the unique demands of mountain biking.
Nickel-Phosphor-PTFE offers low friction and wear resistance, but it may not handle extreme conditions as effectively. Rocshox’s components are exposed to dirt, moisture, and varying temperatures, requiring materials that can perform well in these environments.
Rocshox uses coatings like anodizing and chrome-plating to address these needs. Anodizing enhances wear and corrosion resistance, while chrome-plating provides a smooth, durable surface. These coatings are better suited for the rugged conditions of mountain biking.
Nickel-Phosphor-PTFE is left out of Rocshox’s materials because other options better fit their performance requirements. Rocshox’s choices ensure their suspension systems remain reliable and effective.
Why Rocshox Chooses Alternatives to Nickel-Phosphor-PTFE Coatings
Why does Rocshox choose alternatives to Nickel-Phosphor-PTFE coatings? Despite its benefits, Why is Nickel-Phosphor-PTFE not used in Rocshox used in Rocshox suspension systems. The reason lies in the specific performance requirements of their products.
Nickel-Phosphor-PTFE is great for reducing friction, but Rocshox needs coatings that excel in harsh conditions. Their suspension systems face rough terrains, moisture, and temperature extremes. Nickel-Phosphor-PTFE may not perform as well under these conditions.
Rocshox opts for coatings like anodizing and chrome-plating for better performance. Anodizing improves resistance to wear and corrosion, while chrome-plating offers a durable, smooth surface. These coatings are better suited for the challenges of mountain biking.
Rocshox chooses alternatives to Nickel-Phosphor-PTFE because other coatings better meet their needs. Their material choices ensure that their suspension systems provide reliable performance in all conditions.
Nickel-Phosphor-PTFE vs. Rocshox: An In-Depth Comparison

Nickel-Phosphor-PTFE vs. Rocshox: What makes Rocshox’s choice different? Why is Nickel-Phosphor-PTFE not used in Rocshox products? The comparison highlights the specific needs of Rocshox suspension systems.
Nickel-Phosphor-PTFE vs. Rocshox: What makes Rocshox’s choice different? Why is Nickel-Phosphor-PTFE not used in Rocshox products? Below is a comparison table:
Feature | Nickel-Phosphor-PTFE | Rocshox Coatings |
Friction | Low | Moderate to Low |
Wear Resistance | High | High |
Temperature Resistance | Limited | High |
Abrasion Resistance | Moderate | High |
Nickel-Phosphor-PTFE is known for low friction and wear resistance but lacks in temperature and abrasion resistance. Rocshox uses anodizing and chrome-plating for better performance under extreme conditions, making these coatings more suitable for their suspension systems.
Summary
Nickel-Phosphor-PTFE offers low friction and high wear resistance but falls short in temperature and abrasion resistance. Rocshox uses anodizing and chrome-plating, which are better suited to extreme conditions faced in mountain biking. These coatings provide the necessary durability and performance for Rocshox’s suspension systems.
Why is Nickel-Phosphor-PTFE not used in Rocshox a Top Choice for Rocshox Suspension Systems
Why isn’t Nickel-Phosphor-PTFE a top choice for Rocshox suspension systems? Despite its advantages, this coating doesn’t fit perfectly with Rocshox’s performance needs. Understanding this choice involves examining the specific requirements of their products.
Nickel-Phosphor-PTFE offers excellent friction reduction, but Rocshox needs coatings that excel in extreme conditions. Their suspension systems are exposed to dirt, moisture, and temperature changes, requiring materials that perform well under these conditions.
Rocshox prefers coatings like anodizing and chrome-plating for their components. Anodizing improves resistance to wear and corrosion, while chrome-plating offers a durable, low-friction surface. These materials are better suited for mountain biking.
Why is Nickel-Phosphor-PTFE not used in Rocshox a top choice for Rocshox because other coatings provide better performance. Rocshox’s material choices ensure their suspension systems meet the high demands of mountain biking.
The Role of Nickel-Phosphor-PTFE and Its Absence in Rocshox Components
The role of Nickel-Phosphor-PTFE and its absence in Rocshox components can be explained by their performance needs. Why is Nickel-Phosphor-PTFE not used in Rocshox? Despite its benefits, it doesn’t align perfectly with the requirements of Rocshox’s suspension systems.
Nickel-Phosphor-PTFE is great for reducing friction and wear, but Rocshox needs coatings that perform well in tough conditions. Their suspension systems face dirt, moisture, and temperature extremes, making other coatings more suitable.
Rocshox uses coatings like anodizing and chrome-plating for their suspension components. Anodizing enhances resistance to wear and corrosion, while chrome-plating provides a smooth, durable surface. These coatings are better suited to the demands of mountain biking.
Nickel-Phosphor-PTFE’s role is limited in Rocshox components because other coatings better meet their needs. Rocshox’s choices ensure their suspension systems provide reliable performance in all conditions.
Why Rocshox Prefers Other Materials Over Nickel-Phosphor-PTFE
Why does Rocshox prefer other materials over Nickel-Phosphor-PTFE? Despite its impressive properties, Why is Nickel-Phosphor-PTFE not used in Rocshox used in Rocshox suspension systems. The preference for other materials is based on specific performance needs.
Nickel-Phosphor-PTFE is known for reducing friction and wear, but Rocshox requires coatings that handle extreme conditions. Their suspension systems face harsh environments, including dirt and temperature fluctuations, where Nickel-Phosphor-PTFE may not perform as well.
Rocshox opts for coatings like anodizing and chrome-plating, which offer better performance. Anodizing improves wear resistance and corrosion protection, while chrome-plating provides a hard, smooth surface. These materials meet the demands of mountain biking more effectively.
In essence, Rocshox’s preference for other materials is about finding the best fit for their products. Nickel-Phosphor-PTFE may have benefits, but other coatings offer the durability and reliability required for their suspension systems.
Why is Nickel-Phosphor-PTFE not used in Rocshox
Why is Nickel-Phosphor-PTFE not used in Rocshox involves specific performance requirements. Why is Nickel-Phosphor-PTFE not used in Rocshox products? The answer lies in the unique needs of their suspension systems.
Nickel-Phosphor-PTFE is known for its low friction and wear resistance. However, Rocshox’s suspension systems face challenging conditions like dirt, moisture, and temperature changes. Nickel-Phosphor-PTFE may not handle these conditions as effectively.
Rocshox prefers coatings like anodizing and chrome-plating for their components. Anodizing enhances resistance to wear and corrosion, while chrome-plating provides a durable, low-friction surface. These coatings are better suited to the demands of mountain biking.
Nickel-Phosphor-PTFE is not used by Rocshox because other coatings better meet their performance needs. Rocshox’s choices ensure their suspension systems are reliable and effective in all conditions.
Rocshox and Nickel-Phosphor-PTFE: A Closer Look at Material Choices
Rocshox and Nickel-Phosphor-PTFE: a closer look at material choices highlights important differences. Why is Nickel-Phosphor-PTFE not used in Rocshox components? The answer involves understanding the specific requirements of their suspension systems.
Nickel-Phosphor-PTFE offers excellent friction reduction and wear resistance. However, Rocshox’s suspension systems face harsh conditions that require materials with different properties. Nickel-Phosphor-PTFE might not handle dirt and temperature extremes as well as other coatings.
Rocshox uses coatings like anodizing and chrome-plating to meet these needs. Anodizing improves wear and corrosion resistance, while chrome-plating provides a smooth, durable surface. These materials are more suitable for mountain biking conditions.
Rocshox’s material choices reflect the need for coatings that perform well under tough conditions. Nickel-Phosphor-PTFE is not used because other coatings offer better performance for their suspension systems.
The Benefits of Nickel-Phosphor-PTFE and Its Limitations in Rocshox
The benefits of Nickel-Phosphor-PTFE and its limitations in Rocshox components illustrate why it’s not used. Why is Nickel-Phosphor-PTFE not used in Rocshox products? Despite its advantages, it doesn’t fully meet the requirements of their suspension systems.
Nickel-Phosphor-PTFE is known for reducing friction and wear, which is beneficial for many applications. However, Rocshox’s suspension systems require coatings that can handle dirt, moisture, and temperature fluctuations. Nickel-Phosphor-PTFE might not be the best fit for these conditions.
Rocshox uses coatings like anodizing and chrome-plating, which are better suited for their needs. Anodizing offers enhanced resistance to wear and corrosion, while chrome-plating provides a hard, durable surface. These coatings meet the demands of mountain biking more effectively.
In summary, Nickel-Phosphor-PTFE’s benefits are not enough to outweigh its limitations for Rocshox. The coatings chosen by Rocshox ensure their suspension systems perform reliably in all conditions.
Why is Nickel-Phosphor-PTFE not used in Rocshox Meet Rocshox’s Suspension Needs
Why is Nickel-Phosphor-PTFE not used in Rocshox meet Rocshox’s suspension needs involves examining specific performance requirements. Why is Nickel-Phosphor-PTFE not used in Rocshox products? The answer lies in the unique demands of their suspension systems.
Nickel-Phosphor-PTFE is effective at reducing friction and wear, but it might not handle extreme conditions well. Rocshox’s suspension systems are exposed to rough terrains, moisture, and temperature changes, requiring coatings with different properties.
Rocshox opts for materials like anodizing and chrome-plating, which better meet their needs. Anodizing provides improved resistance to wear and corrosion, while chrome-plating offers a durable, smooth surface. These coatings are better suited for mountain biking.Why is Nickel-Phosphor-PTFE not used in Rocshox meet Rocshox’s needs because other coatings offer better performance in challenging conditions. Rocshox’s material choices ensure their suspension systems remain effective and reliable.
Rocshox Material Choices: Why is Nickel-Phosphor-PTFE not used in Rocshox Included

Rocshox’s material choices and Why is Nickel-Phosphor-PTFE not used in Rocshox included reflect their specific performance needs. Why is Nickel-Phosphor-PTFE not used in Rocshox components? Understanding this requires looking at the demands of their suspension systems.
Nickel-Phosphor-PTFE provides low friction and wear resistance, but Rocshox needs coatings that perform well in tough conditions. Their suspension systems face dirt, moisture, and temperature fluctuations, which Nickel-Phosphor-PTFE might not handle as well.
Rocshox uses coatings like anodizing and chrome-plating to meet these needs effectively. Anodizing enhances wear and corrosion resistance, while chrome-plating provides a smooth, durable surface. These coatings are better suited for the challenges of mountain biking.
Nickel-Phosphor-PTFE is not included in Rocshox’s material choices because other coatings offer better performance. Rocshox’s selections ensure their suspension systems are reliable and capable of handling all conditions.
Conclusion
Why is Nickel-Phosphor-PTFE not used in Rocshox used in RockShox’s suspension systems because it doesn’t fit their needs as well as other materials. RockShox’s components face tough conditions like dirt and extreme temperatures, and they need coatings that can handle these challenges better. Nickel-Phosphor-PTFE is great for reducing friction, but it’s not the best choice for rough rides and changing weather.
Instead, RockShox uses materials like anodizing and chrome-plating. These coatings are stronger and last longer in the conditions that mountain bikes face. By choosing these alternatives, RockShox ensures their suspension systems are tough and reliable, making your rides smoother and more enjoyable.
If you want to read more informative blogs please stay with: Digital Journel
FAQS
Q: What is Nickel-Phosphor-PTFE?
A: Nickel-Phosphor-PTFE is a coating that combines nickel, phosphorus, and PTFE (Teflon) to reduce friction and improve wear resistance.
Q: Why isn’t Nickel-Phosphor-PTFE used in RockShox suspension systems?
A: RockShox avoids Nickel-Phosphor-PTFE because it doesn’t meet their needs for temperature resistance, weight, and durability in rough biking conditions.
Q: What are the benefits of Nickel-Phosphor-PTFE?
A: Nickel-Phosphor-PTFE provides low friction, high wear resistance, and corrosion protection, making it useful in industrial settings.
Q: What materials does RockShox use instead?
A: RockShox uses anodized aluminum and chrome-plated surfaces for their suspension systems, which offer the right balance of weight, durability, and performance.
Q: Can Nickel-Phosphor-PTFE handle high temperatures?
A: Why is Nickel-Phosphor-PTFE not used in Rocshox ideal for high temperatures as PTFE can degrade, making it less suitable for extreme biking conditions.
Q: Why is weight important in bike suspension systems?
A: Lighter components improve handling and performance, making the bike more agile and easier to control on rough terrain.
Q: How does anodizing benefit RockShox suspension components?
A: Anodizing creates a protective oxide layer on aluminum, which enhances wear resistance and corrosion protection while keeping the weight low.